Assurance qualité fournisseur (AQF)
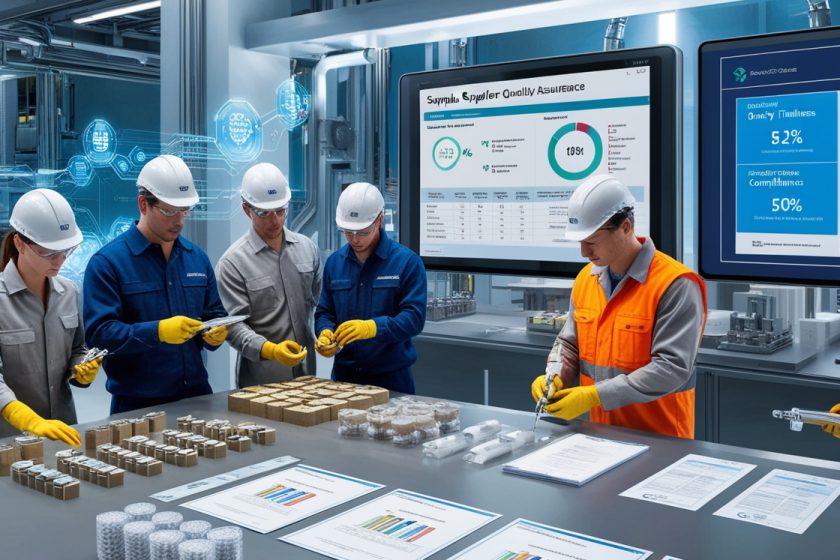
Sommaire
- 1. Principes de l'assurance qualité
- 2. Méthodes d'évaluation de la qualité des fournisseurs
- 3. Processus de sélection et d'évaluation initiale des fournisseurs
- 4. Développement de nouveaux produits avec les fournisseurs
- 5. Gestion des modifications et amélioration continue
- 6. Études de cas et exemples pratiques : Le cas Eramet
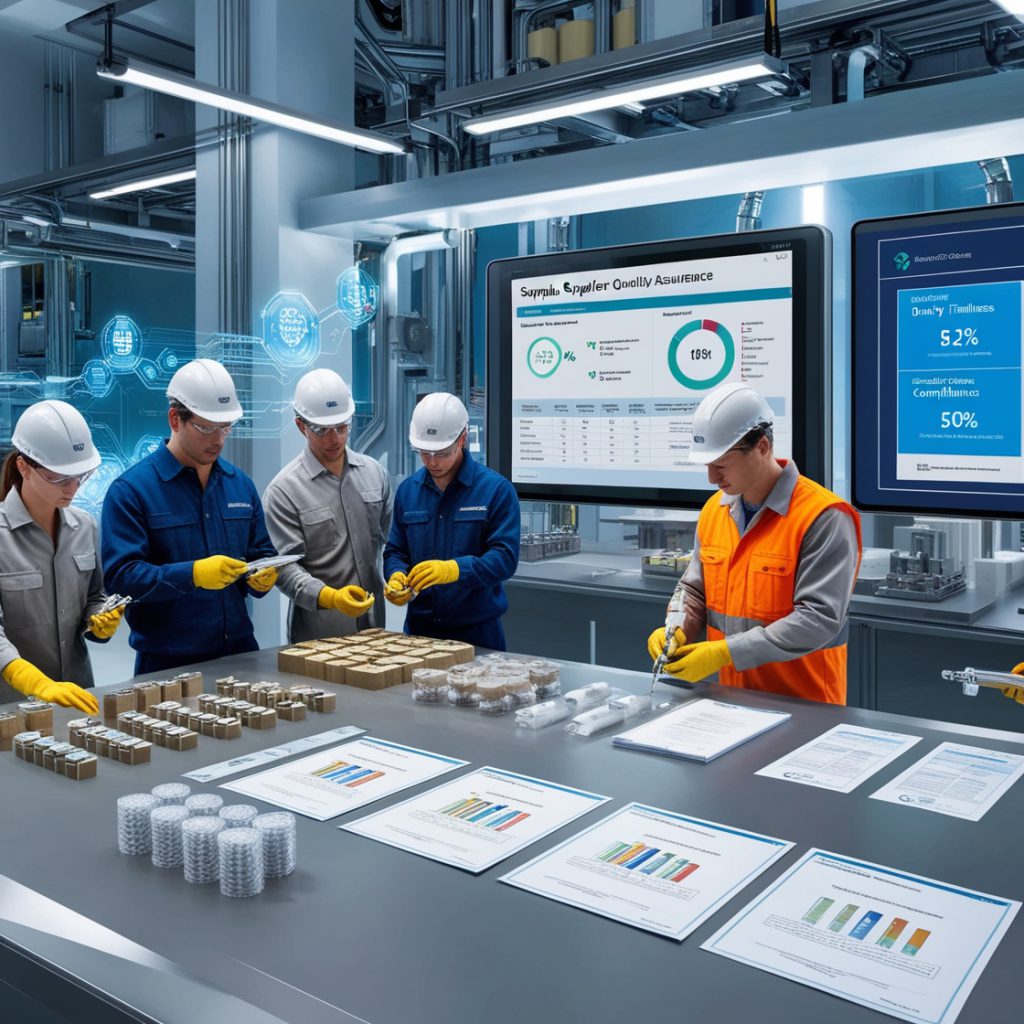
L’assurance qualité fournisseur (AQF) est une composante cruciale de la gestion de la qualité au sein des chaînes d’approvisionnement, particulièrement dans des secteurs exigeants comme l’automobile. Elle vise à garantir que les fournisseurs et les produits satisfont les exigences de qualité et de service des clients. Ce processus systématique aide les entreprises à réduire les risques, à contrôler les coûts de non-conformité et à optimiser la satisfaction client.
L’importance de l’AQF s’étend au-delà de la simple conformité des produits; elle joue un rôle stratégique dans la préservation de la réputation de l’entreprise et dans la garantie de la continuité des affaires. Un système d’assurance qualité efficace aligne les opérations des fournisseurs sur les objectifs de l’entreprise, assurant ainsi une production stable et prévisible.
Principes de l’assurance qualité
L’assurance qualité se distingue par son approche proactive visant à éliminer les sources potentielles d’erreurs dès le début du processus de fabrication ou de service. Cette méthode est basée sur le principe de « prévention plutôt que correction », cherchant à instaurer des pratiques qui garantissent la conformité aux standards de qualité dès les premières étapes de la chaîne d’approvisionnement.
Différence entre qualité et assurance qualité
Tandis que la qualité se réfère directement aux caractéristiques d’un produit ou d’un service qui satisfont les besoins du client, l’assurance qualité représente l’ensemble des actions préventives planifiées pour assurer la constance de cette qualité. C’est un processus continu qui intègre l’évaluation régulière des pratiques en cours et leur ajustement en fonction des retours et des nouvelles exigences du marché.
Méthodes d’évaluation de la qualité des fournisseurs
Pour assurer une qualité irréprochable des produits et services, les entreprises mettent en œuvre diverses méthodes d’évaluation des fournisseurs. Ces méthodes permettent de s’assurer que les fournisseurs respectent les normes de qualité et les exigences spécifiques de l’industrie.
Comment calculer les indicateurs clés de performance liés à la qualité ?
Les indicateurs clés de performance (KPIs) liés à la qualité incluent le taux de réponse aux demandes, la ponctualité de la livraison, et la qualité du produit livré. Pour les calculer efficacement, il est essentiel de définir des critères clairs et mesurables lors de l’établissement du contrat avec le fournisseur. Ces KPIs doivent être régulièrement revus pour s’assurer qu’ils restent alignés avec les objectifs de l’entreprise.
Outils pour évaluer la performance des fournisseurs
L’évaluation de la performance des fournisseurs peut se faire à travers des audits réguliers, des évaluations sur site, et l’utilisation de logiciels spécialisés qui collectent et analysent les données en temps réel. Ces outils permettent de surveiller la conformité des fournisseurs aux exigences contractuelles et d’identifier rapidement les domaines nécessitant des améliorations ou des interventions.
Processus de sélection et d’évaluation initiale des fournisseurs
La sélection et l’évaluation initiale des fournisseurs sont cruciales pour établir une base solide pour la qualité et la fiabilité dans la chaîne d’approvisionnement. Ce processus systématique assure que seuls les fournisseurs qui répondent aux standards de qualité et de performance sont retenus.
Établir un cadre général
Avant de commencer l’évaluation des fournisseurs, il est essentiel d’établir un cadre général qui définit les objectifs et les attentes de l’entreprise. Ce cadre doit inclure les critères de sélection, les méthodes d’évaluation, et les standards de performance attendus.
Identifier les fournisseurs à évaluer
Une liste de fournisseurs potentiels est dressée en fonction de leur capacité à répondre aux exigences spécifiques de l’entreprise. Cette étape peut impliquer des recherches de marché, des recommandations et des pré-évaluations.
Définir la méthode d’évaluation
Les méthodes d’évaluation peuvent varier de simples questionnaires à des audits sur site complets. Le choix de la méthode dépendra de la complexité du produit ou service fourni et de l’importance stratégique du fournisseur.
Déterminer les critères d’évaluation
Les critères d’évaluation doivent être spécifiquement conçus pour mesurer la compétence du fournisseur à livrer des produits ou services qui répondent aux standards de qualité de l’entreprise. Ces critères peuvent inclure la qualité des produits, la fiabilité de la livraison, la capacité de production, et la conformité réglementaire.
Définir les actions à entreprendre
Suite à l’évaluation, des actions spécifiques doivent être prises en fonction des résultats obtenus. Cela peut inclure l’approbation du fournisseur, la demande de modifications ou d’améliorations, ou dans certains cas, le rejet du fournisseur.
Développement de nouveaux produits avec les fournisseurs
Le développement de nouveaux produits en collaboration avec les fournisseurs est une stratégie essentielle pour rester compétitif dans des industries dynamiques comme l’automobile. Cette approche permet de s’assurer que les produits finaux répondent aux exigences de qualité, tout en optimisant les coûts et les délais de mise sur le marché.
Pilotage du projet
Le pilotage de projets impliquant des fournisseurs commence par la définition claire des objectifs, des délais, et des responsabilités. Une communication efficace et régulière est cruciale pour aligner toutes les parties prenantes sur les attentes et les progrès du projet.
Suivi du développement
Le suivi continu du développement permet d’identifier et de résoudre rapidement les problèmes potentiels. Cela implique des réunions régulières, des rapports d’étape et l’utilisation d’outils de gestion de projet pour maintenir tous les acteurs informés des avancements.
Revue de contrat
Les contrats avec les fournisseurs doivent être revus et adaptés régulièrement pour refléter les changements dans les exigences de production ou les normes de l’industrie. Cela assure que les accords restent pertinents et fournissent la base légale nécessaire pour une collaboration efficace.
Prototypes et conformité réglementaire
La création de prototypes est une étape cruciale dans le développement de nouveaux produits. Ces prototypes doivent être testés intensivement pour s’assurer qu’ils répondent aux normes de qualité et aux exigences réglementaires avant la production en série.
Suivi et Évaluation Continue des Fournisseurs
Le suivi et l’évaluation continue des fournisseurs sont essentiels pour maintenir et améliorer la qualité des produits et services tout au long de la relation commerciale. Ces processus permettent d’identifier les problèmes avant qu’ils ne deviennent critiques et de s’assurer que les fournisseurs évoluent en accord avec les standards de l’entreprise.
Suivi de la performance
Le suivi régulier de la performance des fournisseurs à travers des indicateurs clés tels que la qualité des livraisons, le respect des délais et la réactivité aux demandes de changement est vital. Cela permet de mesurer l’efficacité des fournisseurs et d’identifier les domaines nécessitant une attention particulière.
Non-conformités et actions correctives
Lorsque des non-conformités sont détectées, il est crucial de mettre en place des actions correctives de manière rapide et efficace. Cela peut inclure des ajustements dans les processus de fabrication, des formations supplémentaires pour le personnel ou des modifications dans la chaîne d’approvisionnement.
Timing
Le timing des évaluations et des interventions doit être bien planifié pour ne pas perturber l’ensemble de la production. Les audits et les évaluations doivent être programmés à des moments stratégiques pour minimiser l’impact sur les opérations.
Tri
Le tri des produits non conformes doit être effectué de manière à assurer que seuls les produits répondant aux standards de qualité atteignent le client final. Cela peut nécessiter des processus de réinspection et de réparation.
Pénalités
En cas de non-conformité récurrente, il peut être nécessaire d’imposer des pénalités aux fournisseurs pour encourager une amélioration rapide de leurs standards de qualité.
Non-conformité produit récurrente
Les problèmes de non-conformité récurrents nécessitent une analyse approfondie pour identifier les causes racines et mettre en œuvre des solutions durables pour éviter leur répétition.
Traçabilité et conservation des documents
La traçabilité des produits et la conservation des documents associés sont cruciales pour la gestion de la qualité. Elles permettent de retracer l’historique de chaque pièce et d’assurer la conformité avec les réglementations et les standards de l’entreprise.
Gestion des modifications et amélioration continue
La gestion des modifications et l’amélioration continue sont essentielles pour s’adapter aux évolutions du marché et aux exigences réglementaires, tout en améliorant constamment la qualité et l’efficacité des processus de production.
Demande de modification produit / procédé de fabrication
Les demandes de modifications, qu’elles concernent un produit ou un procédé de fabrication, doivent être traitées avec rigueur. Cela implique une évaluation approfondie des implications de chaque changement proposé par le fournisseur, y compris l’impact sur la qualité, les coûts et les délais de livraison.
Modification système
Les modifications des systèmes informatiques ou de gestion utilisés pour le suivi et le contrôle de la qualité doivent être gérées de manière à préserver l’intégrité des données et à assurer la continuité des opérations. Cela peut nécessiter des tests rigoureux et une formation des utilisateurs.
Stratégies d’amélioration continue
L’amélioration continue devrait être un objectif intégré dans la culture d’entreprise. Elle peut être facilitée par des méthodes telles que le Lean Six Sigma, qui aide à identifier et éliminer les gaspillages dans les processus. Des réunions régulières d’évaluation avec les fournisseurs pour discuter des performances et des opportunités d’amélioration sont également cruciales pour maintenir et améliorer la qualité.
Études de cas et exemples pratiques : Le cas Eramet
Dans le cadre de notre exploration des pratiques d’assurance qualité fournisseur, il est instructif de se pencher sur des exemples concrets. Le groupe Eramet, un leader mondial dans le secteur minier et métallurgique, illustre parfaitement l’importance d’une gestion efficace des risques fournisseurs.
Présentation du Groupe Eramet
Eramet opère dans une vingtaine de pays et sur cinq continents, avec un chiffre d’affaires de plus de 3,5 milliards d’euros et environ 13 000 collaborateurs. Le groupe se divise en deux grandes branches : la division minière, qui comprend des opérations de manganèse au Gabon, de nickel en Nouvelle-Calédonie, et de sable minéralisé au Sénégal; et la division alliage haute performance, qui développe des alliages destinés principalement à l’aéronautique et à l’automobile.
Enjeux de la gestion du risque fournisseur chez Eramet
Pour Eramet, la gestion du risque fournisseur est cruciale en raison de la diversité de ses segments d’achat et de ses zones d’activité. Le manager de la performance fournisseur chez Eramet, souligne que sans une bonne connaissance des fournisseurs, il serait très complexe, voire impossible, de gérer efficacement les risques. Ces risques peuvent varier de problèmes financiers et de corruption à des défauts de qualité qui peuvent avoir un impact direct sur la production et la performance globale de l’entreprise.
Stratégie d’intégration d’Axiscope
Pour affronter ces défis, Eramet a choisi de mettre en place Axiscope, un outil dédié à la gestion des informations fournisseur. Cet outil permet à Eramet de suivre en continu une multitude d’informations sur ses fournisseurs, allant de l’identification basique à des données plus complexes comme les sanctions ou les condamnations pour des raisons éthiques. L’utilisation d’Axiscope a donc été essentielle pour permettre une gestion proactive des risques fournisseurs, en assurant une meilleure visibilité et contrôle sur l’ensemble des parties prenantes.
Impact sur la gestion des risques
L’implémentation d’Axiscope chez Eramet a significativement amélioré la capacité du groupe à identifier, évaluer et contrôler les risques fournisseurs. Cela a permis d’assurer une meilleure stabilité dans la chaîne d’approvisionnement et de renforcer la confiance en la capacité du groupe à maintenir une production de qualité, même face à des défis complexes et variés.
Conclusion
L’assurance qualité fournisseur (AQF) est essentielle pour assurer la qualité et la fiabilité des produits. L’exemple d’Eramet illustre comment une gestion efficace peut améliorer la performance globale d’une entreprise, soulignant l’importance des outils spécialisés comme Axiscope pour une gestion proactive des risques.
Ces pratiques de qualité ne visent pas seulement à répondre aux normes réglementaires mais aussi à construire une chaîne d’approvisionnement résiliente, boostant ainsi la satisfaction client et renforçant la compétitivité sur le marché.